Utvecklingen av den nya förbränningsreaktorn har skett i samarbete med metallforskningsinstitutet Swerim på stålföretaget SSAB:s område
i Luleå. Projektet har pågått i drygt ett år och hittills ser det väldigt lovande ut.
– Vi har fått fantastiskt bra resultat och nästa steg blir att diskutera en fullskalig anläggning tillsammans med SSAB, säger Fredrik Nyman, applikationsingenjör på Aga.
Masugnsslam innehåller värdefulla ämnen som järn och kol och skulle därför kunna återanvändas vid stålproduktionen. Problemet är att slammet också består av zink, en metall som vid upphettning kan skapa driftsstörningar och kladda fast på ugnsväggarna.
– Genom att hetta upp masugnsslammet till 1 300 grader i reaktorn separeras zinken via en kemisk reaktion. Stoftet följer med rökgaserna och fångas i filter. Bottensatsen blir en attraktiv slaggprodukt som SSAB kan återföra till sina processer. Stoftet kan användas för att tillverka zink, förklarar Fredrik Nyman.
Gasol i försöken
I projektets testkörningar har i princip all zink som finns i slammet kunnat avskiljas. Reaktorn i försöken har drivits med gasol och syrgas. Andra gasformiga bränslen kan också användas med denna teknik. Den så kallade Oxyfinestekniken är inte ny. Arbetet med att utveckla den har pågått sedan 1990-talet. På senare tid, i takt med stålföretagens arbete att ta hand om och återföra restprodukter, har intresset ökat och utvecklandet av en mer förfinad process har tagit fart, berättar Fredrik Nyman. Efter de lyckade försöken i Luleå spirar optimismen hos Aga.
– Det finns ett stort internationellt intresse för den här typen av reaktor. Även med ny teknik att tillverka stål kommer det att uppstå slam med zink som behöver separeras. Dessutom finns redan i dag stora deponier av masugnsslam som kan återvinnas, säger han.
Slipper slambassänger
Katarina Lundkvist är Swerims projektledare för slamåtervinningen och hon är också mycket nöjd med de försök som har genomförts i pilotprojektet.
– Bakgrunden är att SSAB vill kunna återanvända restmaterial, vilket kan skapa både miljömässiga och ekonomiska vinster. Med den här tekniken har vi stora chanser att minska lagringen av masugnsslam och dessutom kan vi spara jungfruligt råmaterial.
Den svenska stålindustrin genererar cirka 20 000 ton masugnsslam årligen och i dag deponeras detta på industriområdet.
– Om slammet kan återföras till masugnen och återanvändas i stålproduktionen motsvarar det ett minskat behov av 12 000 ton järnmalmpelletts per år, konstaterar hon och till lägger att en stor fördel också är att man inte behöver nyanlägga fler slambassänger för förvaring av slammet.
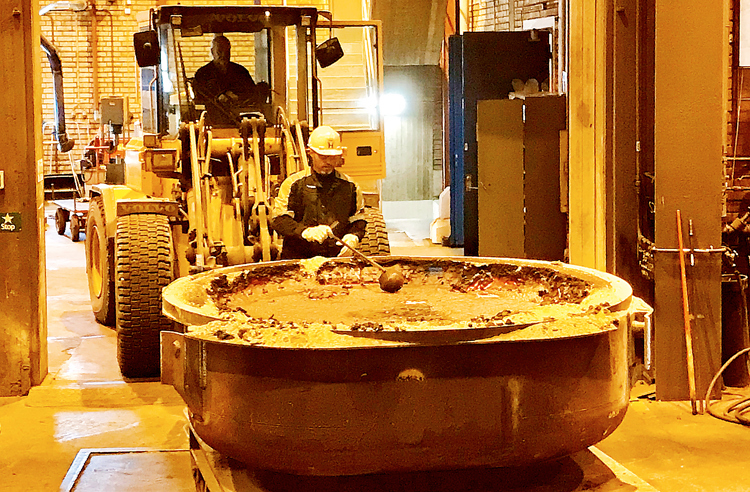
Att återvinna masugnsslammet till 100 procent är bara ett av många forskningsprojekt som pågår i Swerims test- och demohallar intill SSAB:s ståltillverkning i Luleå. Visionen för metallforskningsinstitutet är en fossilfri och cirkulär industri. Stålindustrin står dock inför stora utmaningar för att klara omställningen. Förbränningsprocesserna i stålindustrin orsakar drygt 10 procent av koldioxidutsläppen i Sverige, varav 82 procent av stålindustrins utsläpp kommer från masugnarna.
Stort vätgaslager
Stora förhoppningar står därför till det uppmärksammade forskningsprojektet Hybrit, ett samarbete mellan SSAB, Vattenfall och LKAB. Målet är att kolet i masugnarna ska ersättas med förnybar vätgas. I mitten av oktober invigdes Swerims nybyggda vätgasanläggning ett stenkast från de befintliga test- och demohallarna. Nyligen blev det även klart att det ska byggas ett stort vätgaslager i Svartöberget i Luleå.
– Med Hybrit har vi möjlighet att helt eliminera koldioxidutsläppen och leda arbetet med att utveckla fossilfria stålprodukter. Investeringen i ett lager för fossilfri vätgas är en viktig byggsten för att förverkliga vårt mål att nå en fossilfri värdekedja från malm till färdigt stål, säger Martin Lindqvist, vd och koncernchef på SSAB, i en kommentar.
Lagret ska vara i drift någon gång mellan 2022 och 2024 och beräknas kosta 200 miljoner kronor. SSAB, LKAB och Vattenfall investerar 150 miljoner kronor och Energimyndigheten bidrar med nära 50 miljoner kronor genom Industriklivet.
TEXT: LENA LÄNDIN